Previous post
How to maintain for drone?
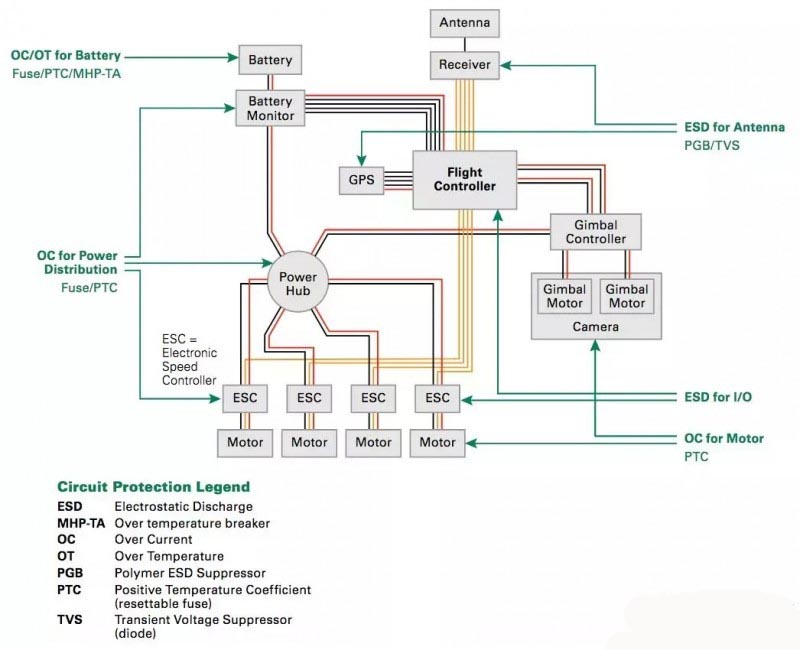
During the flight of the drone, electrical problems are one of the main factors causing the crash, so the electrical protection of the drone is essential. Fortunately, more and more tools and techniques are available for drone battery safety systems, electrostatic discharge (ESD) protection, and stall motor protection.
Figure 1 presents a generic drone design, highlighting some of the areas that drone manufacturers must consider when designing circuit protection for the various electrical subsystems of their products, as well as some of the most common for each application.
Figure 1: Drone subsystem requiring circuit protection
Drones require onboard batteries to power their operations. Lithium-polymer (Lipo) batteries are one of the most common types of batteries used in drones because of their high energy density (related to size and weight), and each battery has a higher voltage, so they can be used more efficiently than other batteries. Rechargeable Batteries A smaller number of batteries power the drone’s onboard systems. They also discharge slower than other types, so they stay charged longer when not in use. However, if not charged or used improperly, they will not provide optimal performance for long periods of time and may even start to smoke and catch fire.
Overdischarge and overcharge are two externally generated events that can cause problems in Li-Ion batteries. During overdischarge, if the cell voltage drops below about 1.5V, the anode will generate gas. When the voltage drops below 1V, the copper from the current collector dissolves, causing an internal short circuit in the cell. Therefore, undervoltage protection needs to be provided by a battery protection IC. When the cell voltage reaches about 4.6V, overcharging creates gas and heat buildup at the cathode. While cylindrical cells have internal pressure protection, activated CIDs (current interrupting devices), and internal PTCs (positive temperature coefficient disks, which increase resistance when heated), LiPo cells do not have internal CIDs and PTCs. External overvoltage, overgas and overtemperature protection are especially important for Li-polymer batteries.
There are a variety of circuit protection options available to help protect drone batteries from overcurrent and thermal conditions, including Metal Hybrid PPTC (MHP-TA) devices with thermal activation, PolySwitch PPTC devices, low resistance SMD PPTC devices and Surface mount fuses. The MHP-TA device combines the advantages of low thermal resistance effect, high holding current rating and compact size, which is very useful for protecting LiPo batteries. The latest MHP-TA devices offer 9VDC ratings and higher current ratings than typical battery thermal cutoffs (TCOs). They are capable of handling the voltages and battery charge rates commonly found in high-capacity LiPo batteries. In the design of ultra-thin battery packs, many provide resettable and precise thermal protection, and their compact form factor and thin size simplify circuit protection.
For other battery chemistries such as Lithium Ion (Li-Ion), Nickel Metal Hydride (NiMH) or Nickel Cadmium (NiCd), PolySwitch PPTC resettable devices offer a better solution. Not only are they compatible with high-volume electronic assemblies, but their UL, CSA, and TÜV agency approvals make it easier for designers to meet regulatory requirements. Their low resistance helps extend battery life and enhances thermal protection.
The small size, low height POLYFUSE LoRho surface mount resettable PPTC is ideal for protection circuit modules for Li-Ion and LiPo battery packs, providing fast overcurrent and thermal protection with ultra-low internal resistance, low voltage drop and power consumption. With automatic reset, they provide a low-maintenance alternative to one-time fuses for overcurrent protection. Because they are packaged for surface mounting on printed circuit boards, they can be installed in electronic protection modules on the circuit board, simplifying the assembly process.
While both fuses and PTCs are overcurrent protection devices, PTCs can reset automatically; traditional fuses need to be replaced after tripping. The fuse will stop the flow of current completely (which may be desirable in critical applications), but after most similar overcurrent events, the PTC will continue to keep the device running, except in extreme cases.
Surface mount fuses like the 449 series NANO2 SLO-BLO subminiature fuse (Figure 2) are widely used in battery charging circuit protection applications. Its unique time-delay feature helps reduce unwanted “false trips” by suppressing inrush currents that cause the fuse to open more quickly.
Cables used to charge drones and drone controllers can also fail electrically. In any charging configuration, the device being charged, the cable and the charger must work together. More and more drones and controllers now feature USB Type-C (USB-C) charging ports. USB-C cables have one or more symmetrical (and therefore reversible) 24-pin connectors. One end of the USB-C charger is an AC plug (for plugging into a power source) and the other end is a cable with a USB-C connector (for plugging into the device to be charged) or a USB-C output port that allows plugging in a USB -C cable.
USB-C cables are susceptible to damage from two different sources. The first issue is the high power levels that these cables must carry when using connectors with very tight pin spacing, which increases the risk of failures that can lead to thermal events. The second problem is that connectors are susceptible to connector pin deformation or contamination from dust, metal particles, hair or other debris, which creates a risk of uncontrolled overheating that can cause resistance from the power line to ground Sexual failure. These resistive faults can cause dangerous temperature rises while increasing the current by only a very small amount. A resistive fault in the USB-C connector can damage the cable and the device being charged.
The latest approach to preventing these destructive resistive failures is to place a protection device in the communication channel (CC) of the USB-C plug, rather than on the VBUS line as was often the case in the past. The compact PolySwitch setP digital temperature indicator (Figure 3) is the latest device designed to protect USB Type-C cables from these overheating conditions. setP detects an increase in temperature and then “warns” the system to power down.
Figure 3 The PolySwitch setP digital temperature indicator helps protect the USB Type-C plug from overheating. They’re designed to comply with USB Type-C specifications and help protect even the highest levels of USB power delivery.
As shown in Figure 1, Electrostatic Discharge (ESD) is a problem for multiple subsystems of drones, including the Global Positioning System (GPS) and receiver antennas and various I/O ports. As these areas form electrical paths for high-potential currents, each access point exponentially increases the risk of immediate and potential damage. For example, the power port is a low voltage input used to charge the battery. As a true DC circuit, a high capacitance value suppressor is recommended. Since this circuit may also experience higher energy transients (lightning, system surge, EFT), a multilayer varistor is recommended because it has a function beyond ESD protection. Additionally, in the event of a persistent overcurrent event (battery failure, circuit failure, etc.), fuses can be used to interrupt the overcurrent condition and protect the system.
Circuit designers can provide antennas with a variety of ESD protection options, including ESD suppressors and TVS diodes. For example, Pulse-Guard ESD suppressors use polymer composites to suppress fast-rising ESD transients (as specified in IEC 61000-4-2) while adding little to circuit capacitance. They complement the on-chip protection of integrated circuits and are best suited for low-voltage, high-speed applications where low capacitance is important to ensure data signal integrity.
TVS (Transient Voltage Suppressor) diodes are designed to protect electronic circuits from transients and overvoltage threats such as EFT (Electrical Fast Transients) and ESD (Electrostatic Discharge). TVS diodes are the typical choice for silicon avalanche devices, usually due to their fast response time (low clamping voltage), low capacitance, and low leakage current. They are available in unidirectional (unipolar) or bidirectional (bipolar) diode circuit configurations. Important parameters to consider when choosing a TVS diode include reverse bias voltage (VR), peak pulse current (IPP) and maximum clamping voltage (VCmax).
ESD is also a concern for I/O ports on flight controllers and electronic speed controllers (ESCs) for flight control motors. The primary consideration for protecting this signal port is the data rate of the signal. As data rates increase, it is critical to consider the capacitance value of the suppressor chosen so as not to introduce any signal integrity issues into the system. For example, circuits in ports operating at low speeds should be protected with higher capacitance multilayer varistors or TVS diode arrays. Likewise, the board designer will decide whether to use discrete MLVs with multi-channel diodes to maintain placement flexibility (discretes) or minimize device count (array products). For very high data rate protocols, suppressors with little capacitance are essential so that the system can transmit and receive data without losing signal quality. Polymer-based ESD suppressors have capacitance values well below 1.0pF and can operate at these higher data transfer rates.
PTC devices are commonly used for overcurrent protection of gimbal motors (which are part of the subsystems that stabilize the image produced by the onboard camera) and flight control motors. Fuses and PTC devices are also frequently used for overcurrent protection of power distribution components such as ESCs, power hubs and battery monitors. TVS diodes are ideal for protecting Wi-Fi antennas/communications ports that handle communications between drones and ground stations.